Commercial Cannabis Production Costs: What’s Included in the Cost to Produce a Pound of Flower?
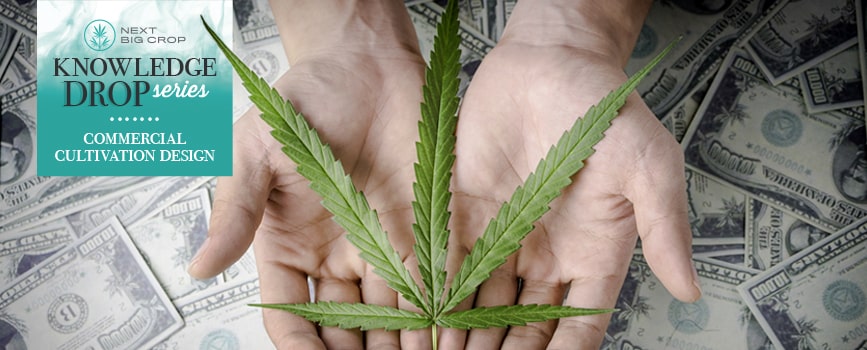
By Christian Phelps, Director of Operations, and Rich Cardinal, Managing Director of Next Big Crop
Read a few articles about the cannabis industry and you will inevitably encounter a bold statement about how it’s going to be worth tens of billions, if not hundreds of billions annually. For business owners and investors, how much of that revenue ends up in your coffers depends largely on your production costs. That includes taxes and cannabis license costs, labor hours and keeping on the (very powerful) lights, among many other aspects.
Knowing how to analyze commercial cannabis production costs will tell you a lot about a business and its cultivators.
Fixed vs. Variable Commercial Cannabis Production Costs
There are two major categories that determine how much it costs to produce a pound of cannabis flower, and knowing how to distinguish between them is crucial to evaluating the performance of cultivators.
Fixed costs are those that the business owner dictates or influences through choices such as location selection. The location of your cultivation site will dictate state and local taxes, employee labor costs, rent expenses, utility prices, etc. These expenses are necessary in calculating the total cost to produce a pound of cannabis, but are typically not able to be significantly manipulated once a location is selected and a building is purchased or leased.
Variable costs, on the other hand, are what the cultivation manager can control: utility (gas, electricity, water) usage, nutrient type and quantity, grow medium, other input materials, labor utilization and the like. Essentially, cultivation managers may not have control over the facility’s total cost per pound, but they do control these variable costs and resulting cannabis yields.
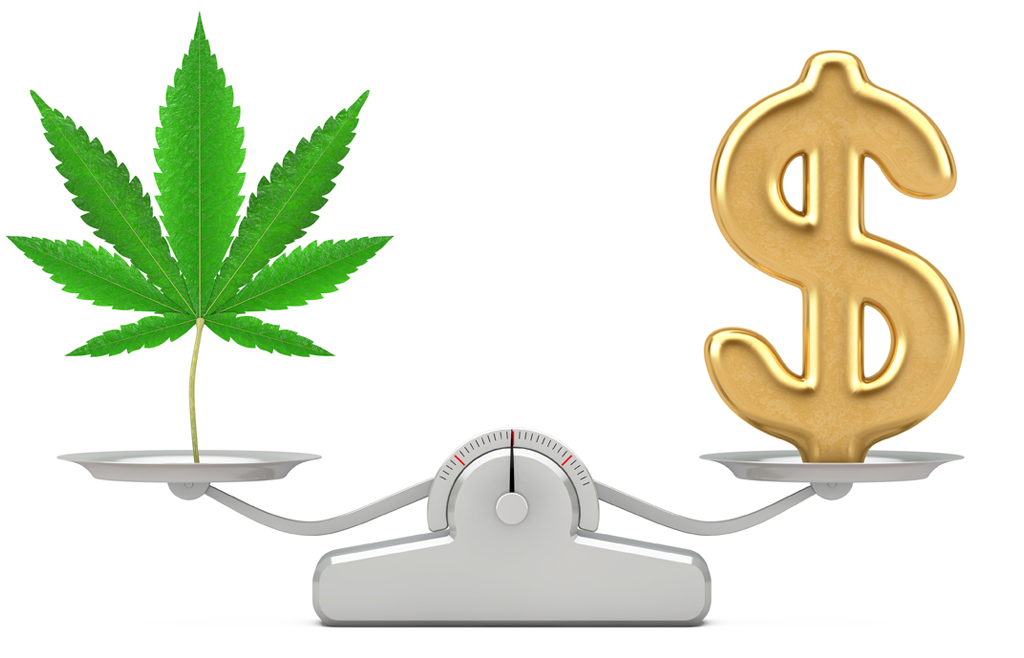
The big question when evaluating cultivation managers is how efficient they are with their space and budget, but this breaks down into lots of little questions. Do they responsibly portion additives to maximize yield and quality, without overfeeding? Is the nutrient lineup and feeding schedule optimized for the plants at each growth stage? Are employees scheduled so that they don’t spend big chunks of their shift standing around? Are your utilities being managed to maximize efficiency without affecting the product that goes out the door? We can get more granular (and hopefully your cultivation manager is obsessing over these questions), but the end result will be influenced by your total variable costs.
Why Do You Ask?
The distinction between fixed and variable costs (for cannabis production, not in the traditional accounting sense) matters when you are evaluating a business versus an individual cultivator.
The business is concerned with the entire picture, from the costs to start a grow operation, cannabis licensing fees, and the particulars of the local and state regulations.
To evaluate a cultivator, focus on the variable costs. Those will give you a broad sense of whether they are being efficient with their resources. That efficiency is what will ultimately drive your profits.
Success Rides on Cultivation Efficiency
An efficient business can produce a pound of cannabis for about $150—or even less—depending on the state and climate. On the opposite end of the spectrum, you could pay as much as $1,000 to grow the same pound of flower. That difference is tied to location and methodology, to be sure, but also cultivation efficiency.
Knowing how to parse fixed costs from variable ones allows you to see just how valuable a cultivator can be. More importantly, you can determine who the great cultivators are, because every successful cannabis business has a top-notch cultivator who is responsibly managing variable costs.
Learn more about Next Big Crop’s operations management and compliance services.
Learn More About Industry Happenings
- Michigan dispensaries, improve online ordering during Coronavirus
- Cannabis Dispensaries Can Adapt to COVID-19 by Offering Delivery and Pickup
- Cannabis Transportation: Business Auto Insurance Vs. Non-Owned and Hired Auto Insurance
- The Future of Cannabis is Female
- 5 Reasons Why Your Dispensary Staff Should be Certified
The bigger question is what exactly is production? Is it the harvests? If so, how do you value what’s in inventory at the end of the period WIP vs. FG? In my experience it’s exceedingly difficult without good data. Would love to hear what others are doing.
Hello
Thanks for sharing