4 Crucial Factors in Maximizing Pre-Roll Production
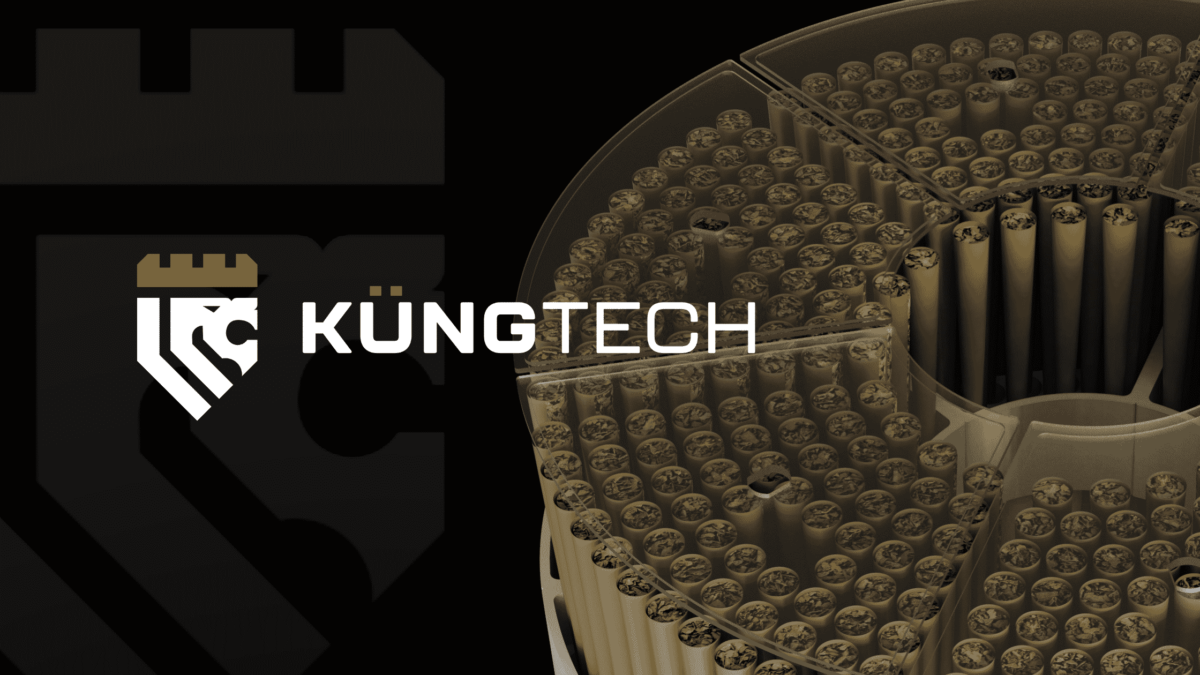
At Kung Tech, we work exclusively with companies that produce pre-rolls, which stands to reason: we make pre-roll machines and other equipment which supports that business. The major driver of our success is understanding what goes into building a thriving pre-roll business, and then working to deliver solutions that overcome the obstacles standing in our clients’ path. Over the last few years, we have probed and prodded our users to understand what factors to focus on to maximize productivity and profitability, and have distilled it down to these four key areas.
Labor
Pre-rolls were once something produced by dispensary workers in their down time. As companies attempted to scale, it often meant throwing bodies – sometimes hundreds of bodies – at the problem; an exercise in brute force that was expedient but not sustainable. Today’s pre-roll producers, with the help of specialized equipment and better processes, have substantially reduced the amount of labor used in the production of pre-rolls, but there is still a lot of fat to be trimmed, and companies will need to continue to live on the leading edge of technology if they want to continue to cut the significant cost of labor. Pre-roll producers must look with a keen eye at every facet of pre-roll production, and determine where steel and circuitry can most adeptly replace brain and brawn. This trade-off is a much easier one to make currently, as the minimum wage rises, avenues for using independent contractors are cut off, and the overall cost of hiring, including taxes and benefits, continues to explode. But, when substituting investment in technology for labor, they must also be cognizant of the downstream effect these changes will have on the other factors listed below. In other words, technological investment must provide a net positive return for the overall business, especially given the enormous cost of some of the equipment in the marketplace. Equipment that produces too many defects, or ones that require constant maintenance and repair due to their complexity, both will sap productivity and necessitate more labor hours (often from highly skilled technicians) than were anticipated. We have seen companies using just two people to produce 20,000 pre-rolls in a day, so we know it can be done. The next steps to take it down from there will be both much harder, and far more interesting.
“We have seen companies using just two people to produce 20,000 pre-rolls in a day”
Quality
No brand, regardless of how productive its operation, will survive without customers. Roll a bad pre-roll, and the world will run away from your door. Too tight, no draw; too loose, draw air. What constitutes quality in a pre-roll is, first and foremost, an engineering problem. Figure out how to construct it even before figuring out what goes into it. There are just a few ways to pack a pre-roll: vibration, compression, and centrifugal force. All rely on physics, but none give you the consistency and packing control you get from harnessing centrifugal force. This consistency and control in packing work together to eliminate canoeing, running, or air pockets to the benefit and delight of the end-user. Finally, quality must also mean the complete eradication of product factors such as cross-contamination and unsanitary production conditions. Producers can achieve this through minimization of labor/”hands” touching the pre-rolls, utilizing easy-to-clean and maintain technology, and thorough production controls.
Precision
With the United States on a path towards full legalization, we can expect the regulatory regime to grow exponentially. Pre-roll producers must be ready to meet this challenge in their operation, or call it a day. Is your technology UL Certified? Ready to stand up to pharmaceutical-level inspection protocols? Can you consistently and efficiently produce pre-rolls within the 5% weight variance level mandated by most states? Is your technology flexible enough to meet the unimaginable new regulations and standards coming down the pike? Are you using a quality, consistent cut in your pre-rolls, which consistency of course impacts so much of what you are trying to achieve? Precision always comes down to erasing the unnecessary from the equation. The best way to do this is to minimize complexity in your technology, with simple, elegant, and adaptable being the winning formula.
Volume
Ask yourself, what would it take to double your output? If the question gives you a headache, you are not alone. That type of growth can quickly turn tiny fissures in your operation into a yawning crevasse. Operators of simple pre-roll systems relying on vibratory packing would put in orders for more machines, wait a few months, hire more people to run the machines while hoping to maintain high quality standards with an untrained workforce. Users who have invested a small fortune in all-in-one technology would probably be reluctant to double down on a new machine, so would hope to tweak production by ramping up their existing equipment. Without backup, and relying on intricate and complicated machinery, operators would be forced to take a risky gamble to maximize output by redlining their machine. In both scenarios, the answer to the question of how you would double your output is not satisfactory. This type of growth in volume requires technology that is both anti-fragile and efficiently scalable.
All these factors combine to benefit the user of your product. For them, they just want to get what they paid for, and the winners will be the ones who can deliver that.